best PCD gear skiving tools
our PCD Gear Skiving Tools combine advanced materials with cutting-edge engineering to meet the demands of high-volume, high-precision production. The use of Polycrystalline Diamond ensures unmatched hardness and thermal conductivity,
1. High rigidity of the machine tool: The feed axis of the machine tool adopts a heavy-duty precision screw with an enlarged diameter to improve the rigidity of the feed.Both the tool axis and the workpiece axis adopt the combination of precision angular contact bearings and double-row four-column roller bearings, which not only guarantees high precision during T rotation but also high rigidity during cutting.
2. Automation technology: The perfect combination of machine tools and automation enables the machine tools to maximize production efficiency.
3. Tool auxiliary replacement: Put the mandrel with the installed tool on the external auxiliary frame, and manually rotate it to the position of the tool spindle.Use the tool change function of the program interface to install the tool in the tool spindle and manually turn it back to the auxiliary frame.
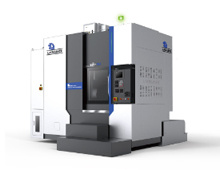
Designed for next-generation gear manufacturing, our PCD Gear Skiving Tools combine advanced materials with cutting-edge engineering to meet the demands of high-volume, high-precision production. The use of Polycrystalline Diamond ensures unmatched hardness and thermal conductivity, allowing the tools to maintain their sharpness and structural integrity even under intense conditions. Ideal for fine finishing of gear teeth and high-speed machining, these tools drastically reduce cycle times and extend tool life compared to traditional carbide options. Their optimized geometry enhances chip control and surface quality, making them ideal for hard-to-machine materials and complex gear profiles.
Suitable for automotive, aerospace, and precision engineering sectors, our PCD gear skiving tools offer consistent accuracy, minimal downtime, and superior cost-efficiency. Trust in our tooling solutions to elevate your gear manufacturing performance with speed, precision, and durability you can rely on.
Recommended Blogs
Revolutionizing Gear Shaping: The Impact of Process Automation
The gear shaping process is a crucial aspect of gear manufacturing, playing a pivotal role in producing high-precision components used in various applications. As the industry continues to evolve, the integration of automation into the gear shaping process represents a significant advancement, offering manufacturers numerous benefits that can enhance their operations. One of the primary advantages
Maximizing Precision: Gear Shaping Through Advanced Automation Techniques
Maximizing Precision: Gear Shaping Through Advanced Automation Techniques Table of Contents 1. Introduction to Gear Shaping and Automation 2. The Importance of Precision in Gear Manufacturing 3. Advanced Automation Techniques in Gear Shaping 4. Key Technological Advancements Driving Automation 5. Benefits of Automation in Gear Shaping Processes 6. Case Stud
Enhancing Efficiency: The Role of Automation in Gear Shaping Processes
In the realm of manufacturing, especially in gear processing machinery, the gear shaping process stands out as a critical operation that directly influences the quality and precision of manufactured gears. However, traditional methods can often be labor-intensive and prone to human error. This is where automation comes into play, revolutionizing the way gear shaping is executed and enhancing overa